برای اطلاع از نخ DTY یکی از ویژگیهای نخهای ترمو پلاستیک[1] قابلیت شکلدهی مجدد به ساختار زنجیرهای پلیمری آن با فرآیند گرم کردن، ایجاد تغییرات ساختاری در زنجیرهای مولکولی از جمله تغییر در مناطق کریستالی و آمورف و سپس تثبیت آن با سرد کردن مجدد است. پارچه های تولید شده با اینگونه نخها به دلیل ساختار لولهای شکل و صاف خود، و لغزندگی و چسبیدن به بدن، و همچنین عدم انتقال مناسب و کافی رطوبت، پوشش مطبوعی ندارند و راحت محسوب نمیشوند. برای استفاده از نخهای فیلامنتی در زمینه پوشاک و نزدیکتر کردن خواص آنها به نخهای تولید شده از الیاف طبیعی و همچنین دستیابی به ویژگیهای مطلوب، لازم است این نخها دارای فر و موج و حلقه (تکسچره) شوند.
امروزه فرآیند تکسچره کردن نخها در صنعت نساجی از اهمیت ویژهای برخوردار شده است. تکسچره نمودن نخهای فیلامنتی گرما نرم سبب بهبود خواص کشسانی، افزایش حجم، افزایش جذب رطوبت و بهبود راحتی پوششی منسوج تهیه شده از آن میگردد. در بین فرآیندهای مختلف تکسچرایزینگ، روش تکسچرایزینگ تاب مجازی رایجترین روش است، به نحوی که تقريبا 76% سهم بازار جهاني نخهای تكسچره شده را به خود اختصاص داده است. در این مقاله به فرآیند تکسچره کردن نخها با روش تاب مجازی، خواص و کاربردهای نخهای تولید شده با این روش پرداخته شده است.
[1] Thermoplastic
فهرست مطالب
روشهای مختلف تکسچرایزینگ تاب مجازی
کاربردهای نخ های تکسچره شده تاب مجازی (DTY)
تکسچرایزینگ نخ فیلامنتی
تکسچرایزینگ فرآیندی است که در آن با استفاده از عملیات مختلف مانند کشش، حرارت، تاب و …. نخ های فیلامنتی مصنوعی از نظر ظاهر، خواص و ویژگی به الیاف طبیعی نزدیک میشوند. روشهای مختلفی برای تکسچره نمودن نخهای فیلامنتی وجود دارد که روش تکسچره جت هوا[2]، تکسچره بافت و شکافت[3]، ایجاد فر و موج با لبه داغ[4]، روش استافر باکس[5] و روش تاب مجازی[6] ازجمله این روشها است. در این میان، روش تکسچرایزینگ تاب مجازی بیشتر مورد استفاده قرار میگیرد.
[2] Air Jet
[3] Knit de knit
[4] Overedge
[5] False twist
Stuffer box [6]
مفهوم تاب مجازی
اگر نخی در دو نقطه ثابت نگه داشته شود و در راستای محور نخ و از وسط نخ، فرآیند تاب دادن انجام شود، تاب نخ در قسمت بالا و پایین یکسان، اما در جهات متفاوت خواهد بود. حال اگر در این حالت نخ در حالت حرکت باشد، تاب نخ بعد از تاب دهنده، تاب نخ قبل از تاب دهنده را خنثی کرده و نخ بعد از واحد تاب دهنده بدون تاب خواهد بود. چنین نخی دارای تاب مجازی است. تصویر تاب مجازی در شکل زیر نشان داده شده است.
اما در تاب حقیقی، به وسیله دوک نخ در دستگاه تابندگی، با توجه به نمره نخ به نخ تاب مشخصی داده میشود و تمامی نخها در یک جهت تابیده میشوند. در ادامه جهت تثبیت تغییر فرم نیز میتوان از دستگاه اتوکلاو استفاده کرد.
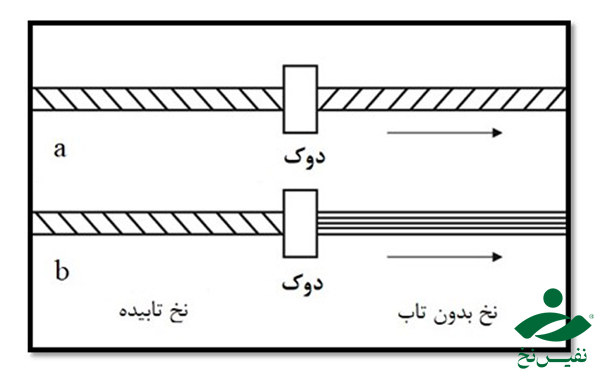
فرآیند تکسچرایزینگ تاب مجازی
نخ تکسچره شده به روش تاب مجازی (DTY)[7] نخ تقریبا آرایش یافتهای است که تحت عملیات تکمیلی، حرارت و کشش قرار گرفته و به روشهای مختلف در آن فروموج[8] ایجاد میشود. فرآیند تکسچرایزینگ تاب مجازی به صورت خلاصه شامل نرم نمودن نخ فیلامنتی یکسره به وسیله حرارت دادن، تغییر شکل نخ نرم شده بهوسیله تاب دادن، خنکسازی نخ در حالت تابدار برای تثبیت تغییر فرم و سپس حذف تاب نخ برای بازگشت نخ به حالت بدون تاب خود است. در این روش، ابتدا با ایجاد کشش و حرارت، ساختار زنجیرههای مولکولی نخ نیمه آرایش یافته (POY) به هم ریخته میشود.
برای آشنایی کامل با نخ poy کلیک کنید.
سپس با تاب دادن به نخ، این زنجیرههای به هم ریخته، در حالت جدید آرایش یافته و حالت زیگزاگی به خود میگیرد. در این حالت، هم زمان عملیات سرد کردن نیز انجام میگیرد. پس از باز کردن تاب نخ، به واسطه داشتن حالت زیگزاگ، نخ حالت فنری و پفکی به خود میگیرد. اجزای مختلف سیستم تکسچرایزینگ تاب مجازی در شکل زیر نشان داده شده است.
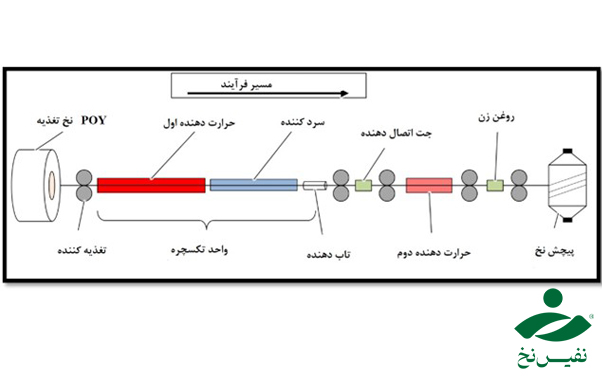
همچنین در شکل زیر از نخ POY و DTY نشان داده شده است:
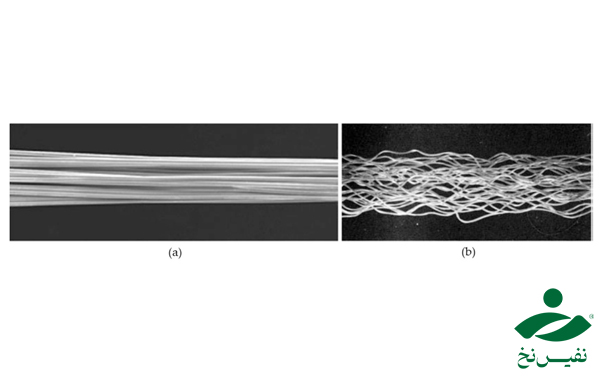
[7] Crimp
Drawn Textured Yarn [8]
[9] Magnetic spindle
[10] Nip Twister
[11] Friction disc
روشهای مختلف تکسچرایزینگ تاب مجازی
بسته به شرایط و روش تولید، روشهای مختلفی نیز برای فرآیند تکسچره کردن نخهای فیلامنتی به روش تاب مجازی وجود دارد؛ از میان آنها میتوان به روشهای تابدهنده آهنربایی[9] ، تابدهنده سوزنی[10] /تسمهای[11] و دیسک اصطکاکی[12] اشاره کرد. در این میان روش دیسک اصطکاکی رایجتر است.
[9] Magnetic spindle
[10] Nip Twister
[11] Friction disc
Apron Belt [12]
ویژگیهای نخ تکسچره تاب مجازی
- نرمی و لطافت بیشتر نخ و منسوجات تهیه شده از آن
- راحتی پوشش، بهبود خواص کشسانی و انعطافپذیری
- بهبود خاصیت آبدوستی و جذب به دلیل ایجاد حالت پفکی در نخ
- عایق گرمایی به واسطه ایجاد فضا بین الیاف
- کاهش درخشندگی نخ
در شکل زیر طرحواره نحوه انعکاس نور از نخهای ساده و نخ تکسچره شده نشان داده شده است. ایجاد فر و موج سبب تغییر زاویه تابش و بازتاب نسبت به هم، شکست بیشتر نور و در نتیجه کاهش درخشندگی نخ میشود.

[5] False twist
بخشهای ماشین کشش تکسچرایزینگ
صرفنظر از سازنده و مشخصات دستگاه، اساس تکسچرایزینگ برای همه ماشینها یکسان است و اجزاء تشکیلدهنده آن عبارتند از:
- قفسه برای نگهداری نخ خام و تغذیه به ناحیه تکسچره
- دو شفت، که بین آنها نخ گرم شده، کشیده شده، خنک شده و از سیستم تاب دهنده عبور میکند.
- دو شفت،که نخ مجدد بین آنها میتواند تحت تغذیه اضافه[13] در گرمکن گرم شود.
- روغن زنی
- جمعآوری و پیچش نخ
[13] Creel
بخش قفسه و تغذیه نخ
کریل[14] قسمتی است كه نخ POY درآن جا قرار میگیرد و نخ از اين قسمت تغذيه میشود. بین قفسه نخ و شفت اول دستگاهی قرار دارد که مجهز به حسگری است که در هر قسمتی از دستگاه که حسگرها پارگی را حس کنند، قیچی نخ را قطع میکند.
جزء بعدی شفت ورودی است که نخ را از قفسه تغذیه به منطقه کشش انتقال میدهد. قابل ذکر است که شفتها در ماشین از یک نوع مشابه هستند. مسئله مهم در ارتباط با حرکت نخ آن است که بدون لغزش از دستگاه عبور کند. به طور معمول واحد انتقال نخ از یک سطح فلز کروم و یک نوار لاستیکی تشکیل شده است. نوارهای لاستیکی ارزان بوده، اما بهآسانی آسیب میبینند.
به منظور جلوگیری از آسیبدیدگی نوار لاستیکی و افزایش طول عمر کارکرد آن، نخها به وسیله یک مکانیزم حرکتی، به طور مداوم در عرض نوار رفت و برگشت انجام میدهند. نبود این سیستم باعث میشود توسط نخ شیاری در سطح نوار ایجاد شود که این مسئله منجر به لغزش و آسیبهای بعدی از جمله پارگی و عیوب نخ میشود.
Overfeed [14]
گرمکن اول
گرمکن اول[15] یا نقش ناحیه حرارتی اول، بالا بردن دمای نخ تابیده شده به یک مقدار مشخص و اطمینان از ثابت ماندن دمای گرمکن و به تبع آن نخ در یک دمای مشخص (بالاتر از دمای انتقال شیشهای و پایینتر از نقطه ذوب) و همچنین یک مدت معین جهت شکسته شدن پیوندهای بین مولکولی تحت تنش است.
[15] Cooling plate
صفحات خنککننده
صفحات خنککننده[16] بین خروجی گرمکن اول و سیستم تاب دهنده قرار دارند و اجازه میدهند که نخ درحالیکه دارای تاب بالایی است، بین خروجی گرمکن اول و ورودی تاب دهنده خنک شود. دمای نخ ورودی به تاب دهنده برای پلیاستر بین 86-90 °c و در واقع بیشتر از دمای انتقال شیشهای (Tg) است. وجود صفحات خنک کننده از منظر پایداری فرآیند تکسچرایزینگ بسیار مهم است؛ زیرا اگر صفحات خنککننده وجود نداشته باشند، نخ که پس از خروج از گرمکن دارای تاب بالایی است ناپایدار شده و تمایل به ایجاد حالت بالون داشته و منجر به افزایش نرخ نخ پارگی میشود. نقش ناحیه سردکننده، تثبیت پیوندهای شکسته شده در منطقه حرارتی اولیه، در موقعیت جدید است.
First heater [16]
واحد تابدهنده
در واحد تابدهنده[17] تاب دادن فیلامنتهای کشیده و گرم شده و سپس باز کردن تابها منجر به موجدار شدن و حجیم شدن[18] نخ میشود. متداولترین واحد تاب دهنده اصطکاکی مجموعه دیسکهای اصطکاکی میباشد. تعداد دیسکها میتواند متفاوت باشد؛ به عنوان مثال ترکیب دیسکها میتواند بهصورت 1-4-1، 1 دیسک ورودی، 4 دیسک اصلی و 1 دیسک خروجی باشد. با افزایش نمره نخ معمولا از دیسکهای ضخیمتر و بیشتر استفاده میشود. جنس دیسکها میتواند سرامیکی، پلی یورتان، نیکل/ الماس و یا سرامیک با پوشش پلاسما باشد. بهطور معمول از دیسکهای سرامیکی و پلی یورتانی استفاده میشود. در شکل زیر سیستمهای تاب دهنده نشان داده شده است.
[17] Twisting unit
[18] Intermingling jet

جت اینترمینگل
از جت اینترمینگل[19] یا جت باد برای ایجاد گره در نخ استفاده میشود. عبور هوا فيلامنتها را در كنار هم نگه داشته و سبب راحتی استفاده از نخ در مراحل و فرآیندهای بعدی مانند چله پیچی، بافندگی و… میشود. گرهها بسته به نوع مصرف و نوع پارچه باید به قدر کافی استحکام داشته و یکنواخت باشند.
مینگلهای شرکت نفیس نخ، بسته به فشار هوا و سرعت عبور نخ (استحکام و تعداد) از جت دسته بندی ميشوند. HH مینگل خیلی قوی، H مینگل قوی، L مینگل متوسط، LL مینگل ضعیف و LLLL مینگل خیلی ضعیف و نخهای ساده بدون مینگل هستند.
Bulk [19]
گرمکن دوم
نخ بعد از عبور از شفت مرکزی، وارد گرمکن دوم[20] میشود. شایان ذکر است که استفاده از گرمکن دوم اختیاری بوده و بسته به خواص نهایی نخ مورد نظر مورد استفاده قرار میگیرد. برای مثال، کاهش مقدار جمع شدگی یا کاهش خاصیت فنریت و استرچ[21] نخ. نخهای استرچ دارای فنریت زیاد و حجم کم هستند، که نقش منطقه حرارتی اولیه و تاب دهنده و منطقه سردکننده تولید نخهای استرچ میباشد. با حرارت مجدد، این نخ تثبیت شده و تنشهای داخلی آن آزاد میشود و در نتیجه فنریت کاهش یافته و حجم بیشتر میشود. منطقه حرارتی ثانویه، خاصیت فنریت نخ استرچ را کاهش داده، باعث افزایش بیشتر حجم بیشتر شده و نخ ست[22] حاصل میشود.
[20] Second heater
[21] Set
Stretch [22]
روغن زنی
برای نخ کشی راحت در دستگاه بافندگی و همچنین برای کاهش اصطکاک بین نخ و قطعات بافندگی و خاصیت الکتریسیته ساکن از روغن استفاده میشود.
محاسبه D/Y و نسبت کشش
نسبت سرعت سطح دیسک به سرعت نخ به نسبت D/Y معروف است که بهصورت زیر محاسبه میشود:

با افزایش D/Y استحکام اندکی کاهش مییابد. D/Y بهطور مستقیم مقدار تاب نخ را تحت تاثیر قرار میدهد. با افزایش D/Y تاب ابتدا زیاد شده و سپس ناگهان لغزش افزایش یافته و تاب کاهش مییابد؛ بهعلاوه با افزایش D/Y مقدار تاب افزایش مییابد و تاب بالا منجر به اغتشاش در بلورها میشود. درنتیجه پایداری موج کاهش مییابد. با افزایش D/Y جمع شدگی موج ابتدا افزایش و سپس کاهش مییابد.
نسبت کشش[23]، نسبت سرعت شفت مرکزی به شفت ورودی است که از رابطه زیر محاسبه میشود:
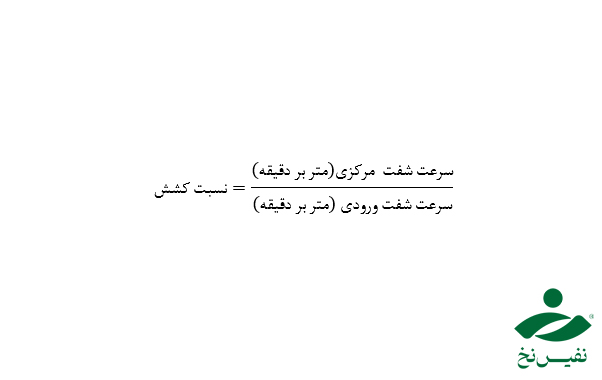
با افزایش نسبت کشش استحکام افزایش مییابد. نخ تغذیه شده نخ نیمه آرایش یافته است، پس کشش در گرمکن اول میتواند آرایش یافتگی مولکولی را بهطور قابلتوجهی افزایش دهد. نسبت کشش نیز دارای مقدار بهینه میباشد. مقدار بیشتر آن باعث پارگی نخ میشود. در شکل زیر تصویری از نخ DTY مینگلدار قابل مشاهده است.
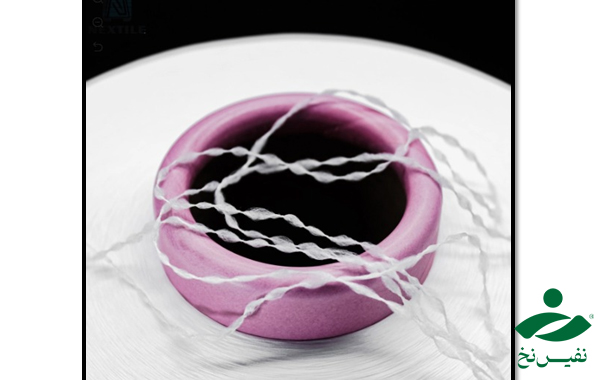
برای اطلاع بیشتر از نخ DTY نفیس نخ کلیک کنید
در شکل های زیر نمایی از ماشین تکسچرایزینگ و بخشهای مختلف آن نشان داده شده است.
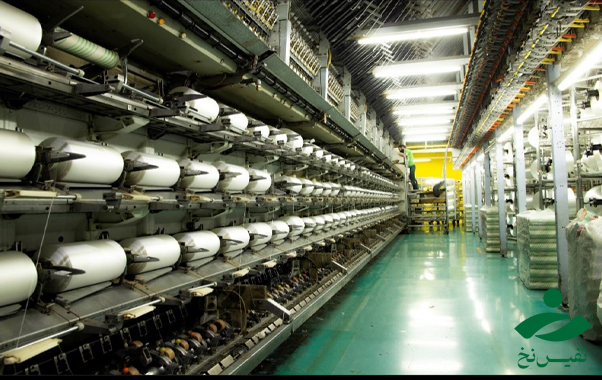

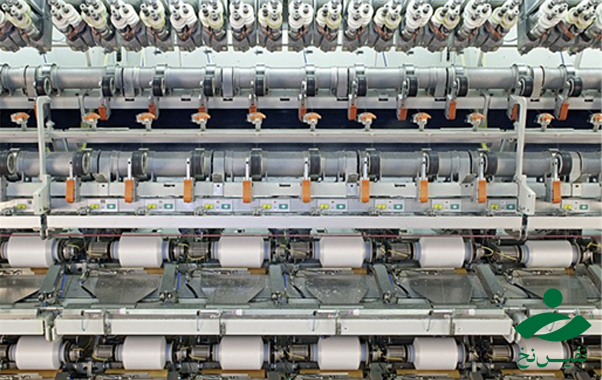
[23] Draw Ratio
کاربردهای نخ های تکسچره شده تاب مجازی (DTY)
همانطور که پیشتر اشاره شد، فرآیند تکسچرایزینگ منجر به ایجاد خواص ظاهری، فیزیکی و مکانیکی مطلوب و متفاوتی در نخهای فیلامنتی میشود؛ این تغییرات باعث تنوع کاربرد این نخها میگردد. در ادامه برخی از کاربردهای این نوع از نخها آورده شده است:
- نخهای با نمره زیر 100 دنیر: پیراهنی، تیشرت، لباس ورزشی، چله شال و روسری، مانتویی (تاری پودی)، جورابی، پردهای، خودرویی (حلقوی تاری و تاری پودی) ، ملحفه، تشک گردبافی.
- نخهای 200-150 دنیر: پیراهنی، دورس، جورابی، پارچه تترون و متقال، ملحفهای، روتختی، پتو مسافرتی، چله پتو، گردبافی تشکی، پشت کار رومبلی، نخهای تار پارچه رومبلی، پزشکی (باند) ، دستکشی ، رویه کفش .
- نخهای 400-200 دنیر: چله سجادهای، چله رومبلی و روفرشی، خاب پتوی راشل، پردهای (تارو پود)، نوار پرده، ملحفهای، روتختی، شبه فاستونی، رویه کفش، چله خودرو، دستکشی، پارچههای صنعتی (چادر برزنتی، فیلتر).
- نخهای 1600-400 دنیر: خاب فرش، چله فرش، پود فرش، سجاده ای، رومبلی، روفرشی، پتویی، پرده زبرا، صنعتی (فیلتر، تسمه، نوار نقاله، چادر برزنتی).
- نخ های استرچ به دلیل فنریت بالا در مواردی همچون جوراب (پوشیدن راحت و به فرم پا درآمدن) استفاده میشوند. نخهای ست خاصیت فنریت کمتری داشته و در مواردی که فنریت کم مورد نیاز است (مثل لباسی) استفاده میشود.
منابع
- توانایی، حسین (1386)، تکسچرایزینگ، اصفهان: نشر ارکان.
2. Ortega, M., Saynisch, A., Yurtseven, B. M., & Gries, T. (2024). A Review on False-Twist Texturing. Fibers, 12(4), 36.
3. Burnip, M. S., Hearle, J. W. S., & Wray, G. R. (1961). The technology of the production of false-twist textured yarns. Journal of the Textile Institute Proceedings, 52(8), P343-P370.
4. False Twist Textured Yarns: Principles, Processing and Applications. (2012).C , Atkinson.
5. Tehran, M. A., Azimi, B., & Mojtahedi, M. R. M. (2011). Investigating the effect of false twist texturing process on the color coordinates variation of spun-dyed polyester filament yarns. Journal of Engineered Fibers and Fabrics, 6(3), 155892501100600307.
6.https://www.fibre2fashion.com/news/textile-news/rieter-acquires-schweiter-s-ssm-textile-machinery-division-206676-newsdetails.htm
7. https://www.directindustry.fr/prod/ssm/product-172529-1778056.html
No comment